The occupational hygiene process incorporates these assessments
- jian lan
- 2021年6月9日
- 讀畢需時 3 分鐘
Prevention of workrelated diseases and injuries affecting the skin requires an assessment of the hazards and the risks associated with performing the work prior to the assignment of protective clothing or equipment. This assessment is legally required in some countries and is typically called a hazard or risk assessment. The assessment should consider the nature and extent of the hazards involved, the likelihood of exposure to hazardous materials or agents, the potential severity of adverse effects of exposure to the worker, solutions other than personal protective equipment, and the overall risk to the user performing the task or work while using protective equipment. The occupational hygiene process incorporates these assessments.
II. RISK ASSESSMENT REQUIREMENTS Some countries, such as the United States, have a legal requirement for a “hazard assessment” prior to the selection and use of personal protective equipment. As an example, the U.S. Occupational Safety and Health Administration (OSHA) regulations (29 CFR 1910.132) require the employer to assess the workplace to determine whether hazards are present or likely to be present, and if so, to select the appropriate protective equipment for the specific hazard(s) involved. It also requires that the selection decision be communicated to the affected employee, that the equipment fit properly, and that training of employees in the use and limitations of the equipment is provided Disposable Aprons.
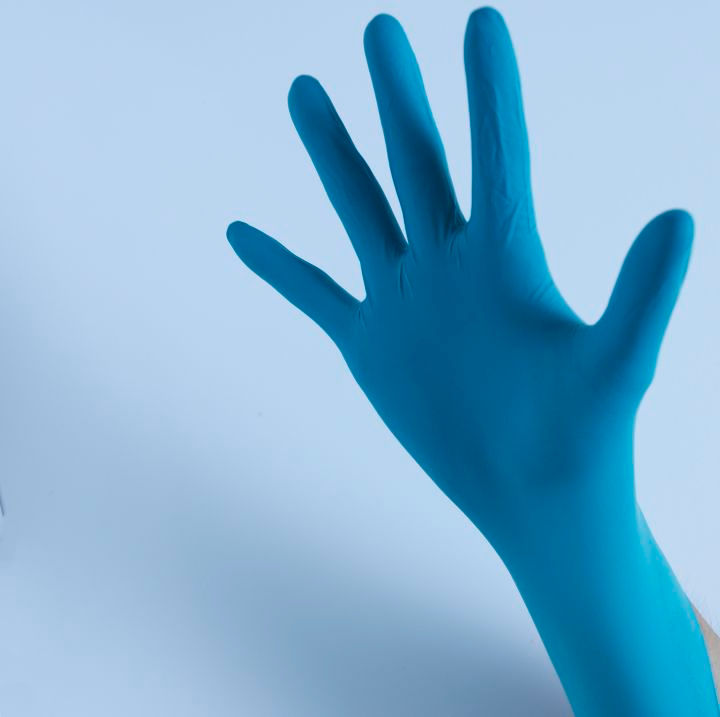
The occupational hygiene process incorporates these required elements of the assessment. III. THE OCCUPATIONAL HYGIENE PROCESS The focus of the art and science of occupational hygiene (also known as industrial hygiene) is the anticipation, recognition, evaluation, and control of chemical and physical agents and other stressors in the workplace and community.1 Anticipation of health and safety hazards based solely on a review of plans for a process, on proposed changes in materials, or on job descriptions alone requires the most sophisticated level of occupational hygiene knowledge and skill. As might be suspected, this skill relies heavily on a mix of experience and knowledge to anticipate potential problem areas before the problems actually occur. The next aspect of the occupational hygiene process—recognition of a problem—is a somewhat less difficult task, although one that still relies a great deal on both experience and knowledge. Many times this phase of occupational hygiene work is focused on employee complaints, reports of injury or illness, and other concrete indicators of potential adverse health effects. Evaluation of the problem follows the recognition phase.
Occupational hygiene evaluations can be either qualitative or quantitative or both. For materials that present a skin hazard, the evaluation will usually be completed on a qualitative basis TPE gloves, as there are no standard measures for quantifying dermal hazards in the workplace.2, 3 The major emphasis of the evaluation phase is the assessment of risk from exposure, followed by the subsequent consideration of controls available to limit the risk to a point that is considered acceptable by both the employer and the worker. One control method common to many applications is the use of personal protective equipment, especially gloves for the protection of the skin and the hands Food gloves.
For most jobs, it is the hands that are most likely to suffer the consequences of contact with a hazardous chemical or physical agent. Further, organizations such as the National Institute for Occupational Safety and Health have recognized skin diseases and disorders as a major occupational health problem.4 Therefore, gloves play a significant role in protecting workers from chemical and physical hazards.
留言